EpiStride CVD System for Silicon Carbide Epitaxy
Introducing EpiStride CVD System for Silicon Carbide Epitaxy
- Veeco’s latest technology for the compound semiconductor market
- Single-wafer, cross-flow chemical vapor deposition (CVD) system for Silicon Carbide (SiC) epitaxy
- Capable of processing wafers of any size up to 200mm
- Available in single- or dual-chamber configurations
- Designed to become a powerful partner for cutting-edge institutions looking to make giant strides in SiC R&D
Scroll down to learn more about EpiStride’s key benefits |
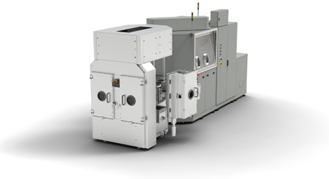 EpiStride system in a single-chamber configuration |
Epitaxial Quality
- Uniform thickness and doping are essential for optimizing device performance, increasing reliability, and improving yield
- EpiStride system can process epi layers of standard 10-15um thickness with industry-leading thickness non-uniformities well below 1% and doping non-uniformities below 2%
- Furthermore, this performance is achieved repeatedly throughout a campaign cycle in-between routine cleaning and maintenance operations
|
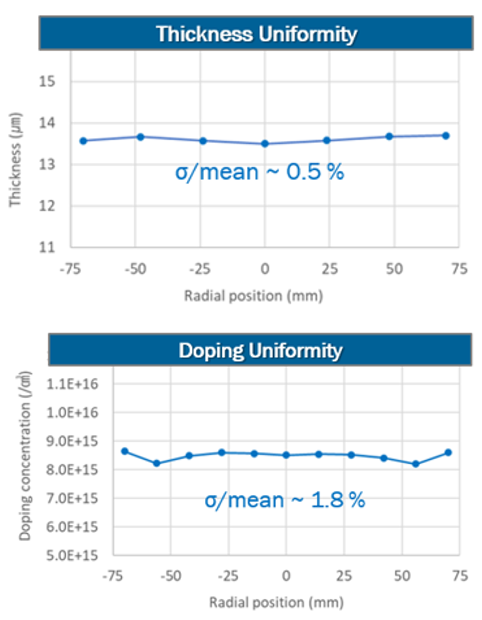 |
Ease of Use
- EpiStride is the only system in the industry that can complete routine cleaning maintenance in less than 5 hours (green-to-green time), with total human touch-time reduced to less than 1 hour
- EpiStride’s Upon completion environment through a glovebox with easy access to the reactor
- EpiStride’s glovebox allows for a quick exchange of parts without complex and time-consuming disconnection of hardware components
- Upon maintenance completion, EpiStride immediately achieves baseline performance without further hardware or software tuning
|
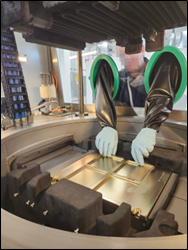 |
Broad Process Window
EpiStride’s approach to temperature and gas flow accelerates process development and improves the repeatability of results.
This unique set of hardware features decouples temperature effects from gas flow effects and enable the broadest process window in the industry, allowing more tuning knobs to be used for the development of new processes for next generation high performance devices.
6 Independent Heating Zones
- EpiStride is the only system that utilizes individually controlled heater zones to tune and optimize the temperature profile of the growth chamber
- The six independent heating zones enable better control of wall temperature upstream and downstream of the wafer as well as control of vertical temperature gradients
- These tuning knobs lead to better temperature uniformity at the wafer surface
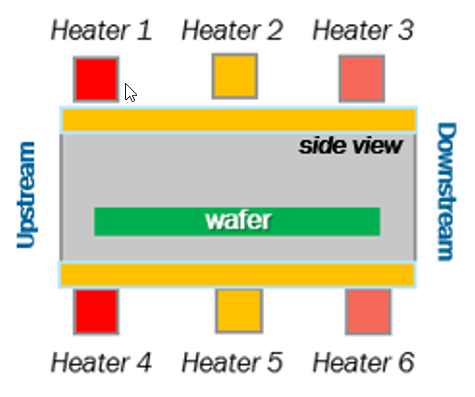
|
3-Zone Gas Injector
- EpiStride’s 3-zone injector allows adjustments of gas concentrations and flows between the center and the edges of the wafer which can lead to better doping uniformity across the wafer
- The flow of nitrogen dopant can be reduced only on the side channels to offset the off-gassing of parasitic deposition near the growth cell sidewalls
- Other possible uses include varying the Carbon-to-Silicon ratio between the center and the edge channels as well as varying the amount of carrier gas flowing through different channels
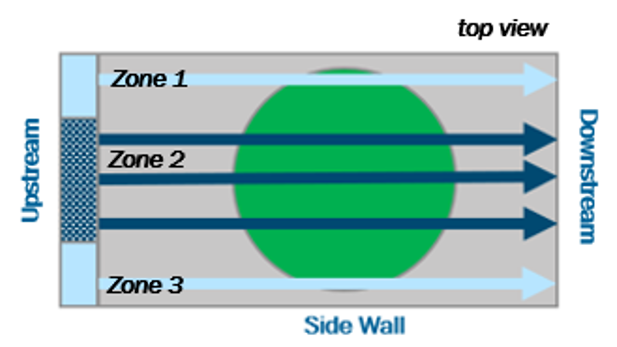
|
Next Generation Capabilities
- EpiStride’s optional 2-reactor configuration can run different dopants in separate chambers to build bipolar epi layers without needing extensive maintenance to change dopants
- The second chamber can also be configured for different materials such as Gallium Nitride (GaN) for exploration of composite epi layers
- EpiStride can run any wafer size without the need for lengthy maintenance periods to upgrade or replace components
- Wafer pre-heating and cooldown stations facilitate more efficient processing by reducing bottlenecks and extreme thermal cycling that increases system wear-and-tear
- EpiStride’s versatility helps ensure that all R&D work can be scaled-up to larger wafer sizes, therefore enabling a quick technology transfer between research and industry
|
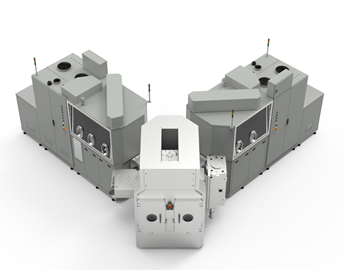 |